銅箔外形激光切割機切不透
好的,這是一份關于銅箔外形激光切割機“切不透”問題的分析報告及解決方案建議,約800字:
銅箔外形激光切割機“切不透”問題深度分析與解決路徑
銅箔作為電子電路、鋰電池等領域的核心基礎材料,其精密加工需求日益增長。激光切割因其非接觸、高精度、高柔性的特點,已成為銅箔外形加工的主流工藝之一。然而,在實際生產中,“切不透”是困擾操作人員的常見且棘手的問題,直接影響產品良率、生產效率和成本。以下針對此問題進行系統分析并提出解決思路:
一、問題核心:能量傳遞與吸收失效
激光切割銅箔的本質是利用高能量密度的激光束局部熔化或氣化材料,配合輔助氣體吹除熔融物形成切縫。出現“切不透”,核心在于到達銅箔表面的有效激光能量不足以克服材料移除閾值,或能量傳遞/吸收過程受阻。具體可分解為以下關鍵環節:
二、根本原因分析(魚骨圖思維:人、機、料、法、環、測)
1.激光源與光路系統(機):
激光功率不足/衰減:激光器老化、泵浦源效率下降、諧振腔污染或冷卻系統異常導致輸出功率低于設定值,無法達到銅箔(尤其是較厚或高純度銅箔)的切割閾值。
光束質量劣化:激光模式不穩定(如TEM00模劣化)、光束發散角過大或存在像散,導致焦點處能量密度不足。常見原因有光學鏡片(透鏡、反射鏡)污染、損傷、熱透鏡效應,或光路準直偏移。
焦點位置偏移:焦點未準確落在銅箔表面或最佳切割焦深區間內(通常略低于表面)。Z軸高度設定錯誤、熱變形、自動調焦系統故障、振動干擾均可導致。
光學元件污染/損傷:切割產生的煙塵、濺射物附著在保護鏡、聚焦鏡表面,嚴重降低透光率。鏡片劃傷或鍍膜燒蝕也會導致能量損失。
2.加工參數設置(法):
切割速度過快:單位長度材料吸收的激光能量不足。
激光功率設置過低:未根據材料厚度、類型、切割速度合理設定。
脈沖參數不當(針對脈沖激光):峰值功率、脈沖頻率、脈寬不匹配,無法有效熔化/氣化銅箔。
輔助氣體問題:
類型錯誤:銅箔切割通常需高純氮氣(N2)以防止氧化,有時也用壓縮空氣(效率較低)。使用氧氣(O2)會形成高熔點氧化銅,更難切透。
壓力/流量不足:無法有效吹走熔融銅液,導致熱量堆積在切口前端形成“熱障”,阻礙后續激光能量進入,甚至造成重凝堵塞切口。
噴嘴問題:噴嘴堵塞、磨損(孔徑變大或變形)、安裝不正(與光束不同軸),導致氣流紊亂、保護氣幕失效、吹除能力下降。
3.材料因素(料):
銅箔厚度超標:實際厚度大于設備/工藝設定的能力范圍。
材料成分/狀態變化:不同批次銅箔的純度、硬度、表面處理(如抗氧化涂層)有差異,影響吸收率和熱傳導。
表面污染/氧化:油污、灰塵、嚴重氧化層增加激光反射和散射,降低吸收率。
張緊力不足/不平整:銅箔在切割區域有褶皺或下垂,導致離焦,能量密度驟降。
4.設備狀態與環境(環、機):
平臺/運動系統精度問題:導軌磨損、絲杠間隙、伺服響應滯后導致實際運動軌跡與設定路徑偏差,部分區域未有效切割。
冷卻系統異常:激光器或光學頭冷卻不足,引發功率保護降額或光學元件熱變形。
環境干擾:強振動(如附近大型設備運行)、溫度劇烈波動影響光路穩定性和設備精度。
氣壓/氣源不穩定:供氣壓力波動導致輔助氣體效果時好時壞。
5.操作與維護(人):
參數設置錯誤:操作員誤輸入參數。
設備維護不到位:未定期清潔光路、更換消耗品(保護鏡、噴嘴)、保養運動部件。
裝夾/對位失誤:材料未正確固定或定位,導致切割位置偏移或離焦。
三、系統性排查與解決方案
解決“切不透”需遵循“從易到難、由表及里”的原則進行排查:
1.快速檢查與基礎調整:
確認參數:仔細核對當前切割程序參數(功率、速度、頻率、氣壓、焦點)是否符合該材料的工藝規范。嘗試小幅降低切割速度或提高激光功率(注意防燒損)。
檢查氣體:確認氣體類型(應為N2)、氣壓/流量是否達標,檢查氣管有無折彎泄漏、過濾器/減壓閥是否正常,清潔或更換堵塞/磨損的噴嘴。
清潔光學窗口:立即檢查并清潔切割頭下方的保護鏡片(遵循嚴格的無塵操作規范)。
檢查材料:確認銅箔厚度、表面是否清潔無氧化、平整無褶皺。清潔表面污漬。
驗證焦點:進行焦點標定測試(如斜坡測試),調整Z軸高度至最佳焦點位置。
2.深入診斷與維護:
檢查光束/光路:使用激光功率計檢測實際輸出功率是否達標。通過專用設備(如光束質量分析儀)或觀察打標/燒蝕效果評估光束模式。系統性地檢查并清潔所有光路中的反射鏡、聚焦鏡(需專業拆卸)。檢查光路準直。
設備狀態檢查:檢查運動系統(導軌、絲杠)潤滑、磨損和間隙。確認冷卻水流量、溫度正常。檢查設備水平及固定是否牢靠,排除環境振動源。
查閱日志/聯系廠商:查看設備運行日志和報警信息。聯系設備制造商技術支持,獲取針對該型號設備的專業診斷建議和可能的參數優化方案。
3.工藝優化與預防:
建立標準工藝庫:對不同厚度、類型的銅箔建立并嚴格驗證最優切割參數組合。
實施預防性維護計劃:定期(按小時或批次)清潔保護鏡片、更換噴嘴;定期(按周/月)檢查清潔內部光路、保養運動部件、校準焦點和光路;定期(按年)檢測激光功率和光束質量。
控制環境與物料:確保工作環境清潔、溫濕度適宜、無強振動。嚴格管控來料銅箔的規格和存儲條件。
操作員培訓:強化操作員對設備原理、參數意義、日常點檢、基礎故障識別的培訓。
四、結論
銅箔激光切割機“切不透”是一個多因素綜合作用的結果。解決該問題不能僅靠單一調整,而需進行系統性排查,從參數設置、輔助氣體、光學系統清潔、焦點校準等基礎環節入手,逐步深入到設備狀態、光路質量和工藝優化層面。建立并嚴格執行標準化的操作流程、工藝參數庫和預防性維護計劃是防止問題復發的關鍵。對于復雜或持續存在的問題,務必尋求設備制造商專業技術支持,利用其專業工具和經驗進行深度診斷修復。通過科學分析和嚴謹執行,可有效解決“切不透”難題,保障生產的連續性和產品的高質量。
(字數統計:約850字)
補充說明:
本報告基于通用原理分析,具體到某一臺設備(如您提到的“250604212”可能是設備編號或訂單號),還需結合該設備的具體型號、配置、使用歷史、當前報警信息等進行針對性診斷。
實際操作中務必遵守激光安全規范,清潔光學元件和調整光路時需特別小心,避免損傷或造成人身傷害。
如果經過基礎排查仍無法解決,強烈建議聯系設備供應商的售后服務工程師進行現場診斷和維修。
點擊右側按鈕,了解更多激光打標機報價方案。
相關推薦
激光切割機切銅板
激光切割機切銅板
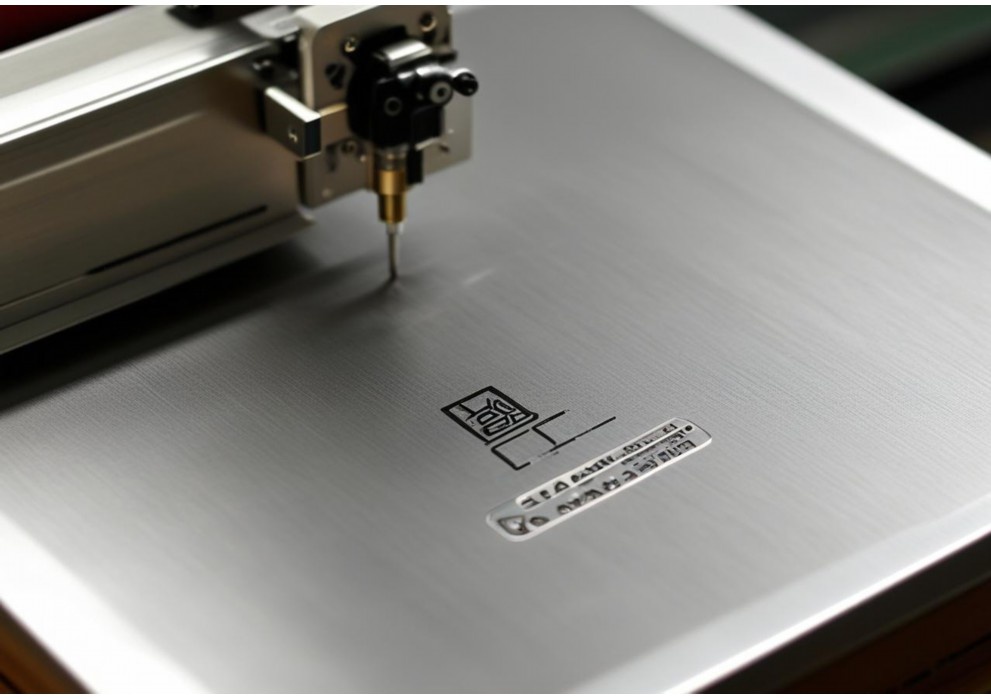
激光切割機高效切割銅板:工藝要點與應用解析
銅板因其優異的導電性、導熱性和延展性,廣泛應用于電力電子、散熱器、裝飾等領域。激光切割作為精密加工手段,在銅板加工中展現出獨特優勢,但也面臨特殊挑戰。
一、銅板激光切割的獨特挑戰與應對
高反射率陷阱:銅對常用紅外激光(如1μm光纖激光)反射率極高(>90%),導致大量能量損失,切割困難。
導熱性難題:銅散熱極快,熱量難以在切口處有效聚集,影響切割效率和斷面質量。
粘渣與毛刺:熔融銅粘性大,易附著在切口下方形成難以清除的熔渣和毛刺。
針對性解決方案:
高功率激光破局:采用≥3kW高功率光纖激光器(推薦6kW以上),以強度克服反射。
抗反射技術加持:使用綠光(532nm)或紫外(355nm)激光器,銅對其吸收率顯著提升(綠光吸收率約40%)。
工藝參數精調:優化焦點位置(常置于板面以下)、峰值功率與占空比(如使用脈沖模式)、氣壓控制(高純氮氣輔助吹渣)。
二、核心工藝參數與設備要求
(典型參數參考表)
|銅板厚度|激光功率|切割速度|輔助氣體|噴嘴類型|焦點位置|
|-||||||
|0.5mm|1-2kW|8-15m/min|高純氮氣(≥15bar)|小口徑(1-1.5mm)|板面下0.2mm|
|1mm|2-3kW|5-10m/min|高純氮氣(≥18bar)|小口徑(1-1.5mm)|板面下0.3mm|
|2mm|≥4kW|2-5m/min|高純氮氣(≥20bar)|特殊防濺射噴嘴|板面下0.5mm|
|3mm+|≥6kW|<2m/min|高純氮氣(≥25bar)|專用抗反光噴嘴|板面下1mm|
設備關鍵要求:
1.高功率高亮度激光源:光纖激光器(IPG、nLIGHT等)為主流。
2.動態調焦系統:實時補償熱透鏡效應,保持焦點穩定。
3.防反射保護裝置:防止反射光損壞激光器光學元件。
4.高穩定性氣路系統:確保氣壓恒定,有效吹除熔融物。
三、優勢應用場景
精密電子元件:FPC柔性電路板補強鋼片、引線框架(切縫<0.1mm)。
高效散熱系統:服務器/IGBT水冷板流道(復雜異形孔無毛刺)。
新能源電池制造:鋰電池極耳(銅箔)無接觸切割(熱影響區<50μm)。
建筑裝飾藝術:紫銅屏風、浮雕(精細圖案無變形)。
四、質量控制與安全要點
斷面質量控制:監測毛刺高度(應<板厚5%)、檢查背面無熔渣粘連(通過調整氣壓和速度優化)。 防氧化處理:切割后及時清潔表面氮化物殘留,必要時做鈍化保護。 嚴格防護措施:安裝防反射罩、佩戴專用防護眼鏡(防銅蒸氣及強反射光)。 實時監控系統:配備CCD視覺或紅外熱像儀,監測切割過程穩定性。 總結: 激光切割銅板是技術密集型工藝,成功的關鍵在于高功率激光源選擇、抗反射技術應用、氮氣輔助工藝優化及精密參數控制。隨著高亮度綠光激光器等技術進步,銅及高反材料的切割效率與質量將持續提升。企業在引入該工藝時,需結合自身產品厚度和精度需求,選擇適配設備并建立嚴格工藝規范,方能充分發揮激光切割在銅加工領域的精密、高效與柔性優勢。 >實踐建議:對于厚度>3mm的純銅板,可考慮”激光-水刀復合切割”或”銑削后激光精修”工藝以平衡效率與質量。持續監控鏡片污染狀況(銅蒸氣沉積)是保障長期穩定生產的關鍵細節。
點擊右側按鈕,了解更多激光打標機報價方案。
如何用激光切割機切割銅板
如何用激光切割機切割銅板
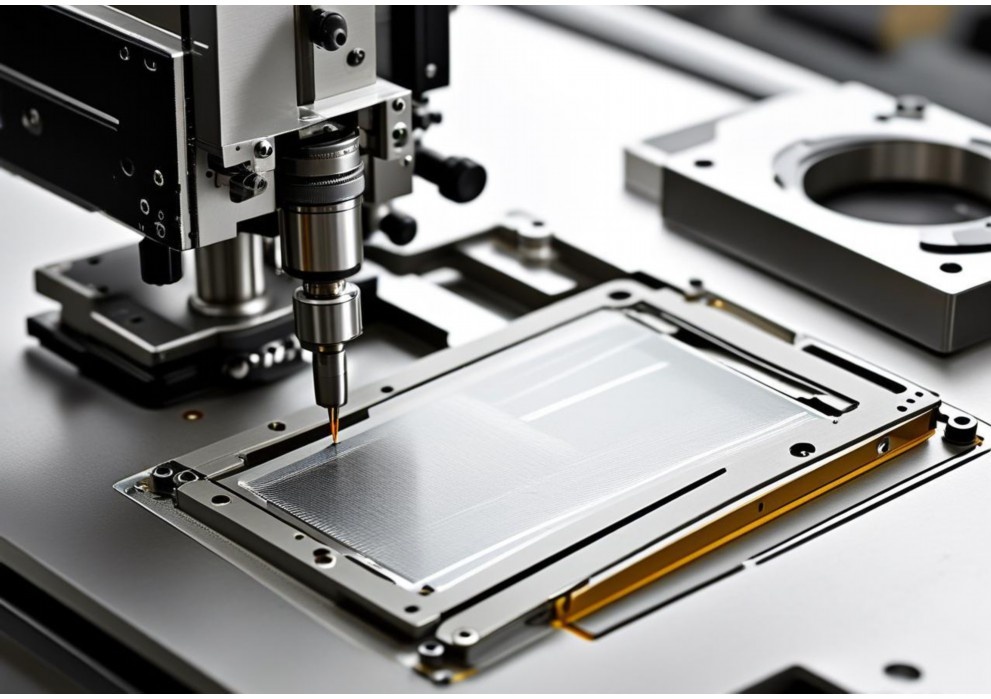
激光切割機切割銅板:專業指南與技巧
銅板憑借其優異的導電性和導熱性,廣泛應用于電子、散熱器、裝飾及工業領域。激光切割因其高精度和無接觸特性成為銅板加工的理想選擇,但銅的高反射率和高導熱性也帶來獨特挑戰。以下為使用激光切割機切割銅板的詳細步驟與關鍵要點:
一、核心設備要求與安全準備
1.激光器類型:光纖激光器
必須選擇光纖激光器(波長1070nm左右)。CO2激光器(波長10.6μm)絕大部分能量會被銅表面反射,效率極低且極易損壞激光器。
功率選擇:薄板(<1mm)可用500W-1000W;中厚板(1-3mm)推薦1500W-3000W;厚板(>3mm)需3000W以上高功率激光器。
2.安全防護:重中之重
反射防護:銅的強反射性是最主要風險。確保切割頭配備高質量、針對銅反射優化的防護鏡片(通常為銅金膜鏡片),并定期檢查更換。
操作員防護:佩戴專用激光防護眼鏡(針對光纖激光波長)。
設備防護:激光器腔體和切割頭內部需有完善的反射光監測與防護機制。
環境安全:清理易燃物,保證良好通風(銅切割產生金屬粉塵和少量煙霧)。
二、切割前準備
1.材料處理:
清潔表面:去除油污、氧化物、保護膜,確保表面潔凈干燥。污漬會導致切割不均勻和反射異常。
提高吸收率(可選但推薦):
涂層法:在切割區域均勻噴涂薄層激光增透材料(如專用黑色標記漆)。
氧化法:對表面進行輕微氧化處理(需控制程度)。
覆膜法:粘貼專用激光吸收膜(效率高,成本稍高)。
平整度:確保銅板平整,避免因翹曲導致焦點偏移或碰撞噴嘴。
2.設備檢查與設置:
聚焦鏡片清潔:無塵環境操作,用專用工具清潔鏡片。
噴嘴選擇與校準:
根據板材厚度選擇噴嘴孔徑(通常薄板用較小孔徑如Φ1.0-1.5mm,厚板用較大孔徑如Φ2.0-3.0mm)。
精確校準噴嘴高度(至關重要?。菏褂谜{高器或塞尺設定噴嘴到板材表面的距離(通常在0.5-1.5mm范圍),確保同心度和氣流穩定。
氣體選擇與連接:
必須使用高純度氮氣(N2)作為切割輔助氣體(純度≥99.999%)。氧氣(O2)會導致銅劇烈氧化,切口發黑、粗糙、產生大量熔渣。
檢查氣路密封性,連接穩定。
焦點位置設定:
焦點位置對切割質量(尤其是垂直度和粗糙度)影響顯著。通常焦點位于板材表面或略微進入板材內部(負離焦)效果更好(例如-1mm到-2mm)。
需通過試切確定最佳焦點位置。
三、關鍵切割參數設置與優化
參數需根據激光器功率、銅板厚度、切割速度、噴嘴、氣體壓力綜合調整。以下為參考范圍(務必以實際設備試切為準):
|參數|薄銅板(<1mm)|中厚銅板(1-3mm)|厚銅板(>3mm)|備注|
|:–|:–|:|:–|:|
|激光功率|500W-1000W|1500W-3000W|3000W+|功率不足無法有效熔融,過高易過燒|
|切割速度|較高(5-15m/min)|中等(2-8m/min)|較低(0.5-3m/min)|速度過快切不透,過慢導致熱影響區大、掛渣|
|氮氣壓力|較高(10-20bar)|高(15-25bar)|非常高(20-30+bar)|壓力不足無法有效吹走熔融物,保證切口清潔|
|焦點位置|表面或略下(-0.5mm)|板材內(-1mm~-2mm)|板材內(-2mm~-3mm)|負離焦增加能量密度,改善厚板切割能力|
|噴嘴高度|0.8-1.2mm|1.0-1.5mm|1.2-2.0mm|確保氣流順暢,避免碰撞|
|穿孔參數|低功率/短時間脈沖|脈沖穿孔或漸進穿孔|必須使用漸進穿孔|尤其重要!防止高反射熔融物飛濺損壞噴嘴/鏡片|
穿孔技巧(關鍵難點):
避免直接高功率連續穿孔:極易引起高反射熔融物劇烈飛濺。
推薦方法:
脈沖穿孔:使用較低功率的脈沖激光逐步“啄”穿材料。
漸進穿孔:激光功率由低到高緩慢增加,同時輔助氣體壓力也逐步提升,直至穿透。這是最安全有效的方法。
穿孔位置盡量遠離輪廓起點一小段距離。
四、操作流程
1.軟件準備:導入或繪制切割圖形,合理排樣,設置切割路徑(引入引出線)。
2.裝夾固定:使用夾具(磁性、機械式)或專用切割平臺(如蜂窩板)牢固固定銅板,防止移動或振動。
3.設定起點與高度:將切割頭移動到板材起始位置,啟動調高器自動探測并設定初始高度。
4.啟動切割:確認所有參數和安全措施無誤后,啟動切割程序。密切監控初始穿孔過程。
5.過程監控:觀察切割火花狀態(應穩定向下噴射)、聽氣體聲音是否穩定、注意是否有異常反射光或報警。
6.完成與取件:切割完成后,待平臺冷卻(尤其是薄板易燙手),小心取下工件,注意鋒利邊緣。檢查切割質量。
五、常見問題與解決方案
1.切不透/速度慢:
功率不足→提高功率(需在設備能力范圍內)。
速度過快→降低切割速度。
焦點位置錯誤→調整焦點(通常向負離焦方向試)。
氣體壓力不足/純度不夠→檢查氣源、管路,提高壓力,確保氮氣純度。
噴嘴堵塞/損壞→清潔或更換噴嘴。
2.切口粗糙/掛渣多:
氣體壓力不足或純度低→提高壓力,確保高純氮氣。
速度過快或過慢→優化切割速度。
焦點位置不佳→調整焦點位置。
功率不合適→微調功率(過高可能使熔池紊亂)。
3.切縫過寬/垂直度差:
焦點位置不準→精確調整焦點。
噴嘴孔徑過大→嘗試更小孔徑噴嘴。
氣壓過高→適當降低氣壓。
4.反射損壞噴嘴/鏡片(最嚴重):
穿孔參數/方法錯誤→必須使用脈沖或漸進穿孔!
噴嘴高度設置錯誤(過低)→重新校準噴嘴高度。
鏡片污染或損壞→立即停機檢查更換鏡片。
材料表面極度不平或有突起→確保板材平整。
設備防反射機制失效→聯系設備廠商檢修。
六、提升切割質量與效率的附加建議
表面預處理:使用涂層、氧化或覆膜法顯著提高激光吸收率,可有效降低所需功率或提高速度,改善切割質量。
高質量耗材:使用原廠或高規格的保護鏡片、噴嘴、聚焦鏡。
優化切割路徑:減少空程移動,合理規劃切割順序減少熱變形。
定期維護:嚴格按手冊清潔光路(鏡片、光纖接頭)、檢查冷卻系統、校準設備。
小批量試切:對于新材料或高要求工件,務必先用邊角料進行參數測試和優化。
總結
成功使用激光切割銅板的核心在于:選用光纖激光器、嚴防反射風險、必須使用高純氮氣、精確設置焦點與噴嘴高度、掌握安全的漸進穿孔技術、根據板材厚度精細調參(功率、速度、氣壓)。通過嚴格的設備維護、規范的操作流程和不斷的參數優化,激光切割能夠為銅板加工提供高效、精密、高質量的解決方案。安全始終是第一要務,尤其在處理高反射材料時。
點擊右側按鈕,了解更多激光打標機報價方案。
激光切割機為什么不能切銅
激光切割機為什么不能切銅
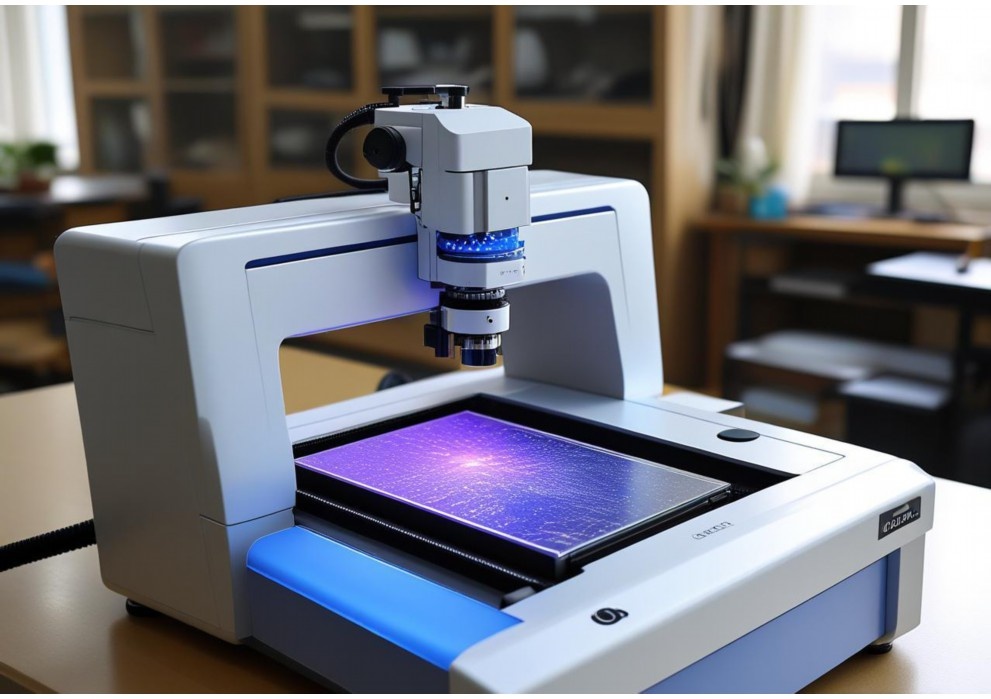
激光切割機“難啃的硬骨頭”:為什么切割銅如此棘手?
在金屬加工領域,激光切割機以其高精度、高效率和高靈活性成為行業利器。然而,當面對銅這種常見金屬時,激光切割機卻常常顯得“力不從心”,甚至完全無法勝任。這背后并非設備能力不足,而是銅材料特殊的物理性質與激光作用機制之間產生了難以調和的矛盾。深入探究這些矛盾,能幫助我們理解技術局限,并找到更合適的加工方案。
一、核心挑戰:銅對激光的“頑固抵抗”
銅對激光的“不合作”態度,源于其一系列獨特的物理特性:
1.超高的反射率:
銅,尤其是純銅和黃銅(銅鋅合金),擁有極高的可見光與紅外光反射率。對于工業激光切割主力軍——波長為10.6微米的CO2激光和1微米左右的光纖/碟片激光——銅在室溫下的反射率普遍超過90%,甚至高達95%以上。
后果:絕大部分入射激光能量被直接反射出去,無法有效進入材料內部轉化為切割所需的熱能。這就像試圖用強光照射一面鏡子,光會被反射走而無法加熱鏡子本身。
2.卓越的導熱性:
銅是地球上導熱性能最好的金屬之一,其熱傳導速度遠超鋼鐵等常用激光切割材料。
后果:即便有少量激光能量被吸收轉化為熱量,這些熱量也會以驚人的速度從激光作用點向四周和材料內部快速擴散。這使得局部區域難以積累起達到銅熔點(約1083°C)所需的、足夠集中的高溫。熱量“瞬間”被傳導走,無法有效熔化材料。
3.較高的熔點與特定的熔化特性:
銅的熔點雖然低于鋼鐵,但結合其高反射率和高導熱性,要達到并維持熔化狀態仍然困難。
后果:熔融銅的粘度較低,流動性好。在切割過程中,輔助氣體(如氧氣、氮氣)難以有效地將熔融銅從切縫中穩定、連續地吹走。熔融物可能飛濺、粘連或重新凝固在切縫壁或切割頭下方,導致切割面質量差(粗糙、掛渣多)、切縫不規則甚至切割中斷。
二、安全風險:致命的反射光
銅對激光的強反射特性不僅導致切割困難,更帶來了極其嚴重的安全隱患:
隨機反射路徑:被銅表面反射的高能激光束方向完全不可預測。
設備損壞:反射光可能直接擊中并燒毀激光切割頭內部精密的聚焦鏡片、傳感器或其它光學元件,造成昂貴的設備損壞。
火災風險:反射的激光束可能擊中切割機工作艙內的易燃材料(如電纜、油污、紙張、護罩),引發火災。
人身傷害:如果防護裝置失效或操作不當,反射的激光束甚至可能穿透工作艙逸出,對操作人員或其他在場人員造成嚴重的眼睛或皮膚灼傷,這種傷害往往是永久性的。這是限制激光切割機加工銅的最重要安全考量之一。
三、技術折中與局限應對
面對銅的挑戰,工程師們也發展出一些應對策略,但都存在顯著局限:
1.使用高功率光纖/碟片激光器:
原理:1微米波長的近紅外激光被銅的吸收率(尤其在熔融狀態下)略高于10.6微米的CO2激光(可能從5%提升到30-40%,但仍遠低于鋼鐵)。超高功率(如6kW,8kW甚至更高)可以在一定程度上克服反射和導熱損失。
局限:
反射風險依然嚴重存在,仍需極其嚴格的防護措施。
主要用于薄銅板(通?!?mm),切割較厚銅板(>5mm)時,效率急劇下降,質量難以保證,切縫寬且粗糙。
設備成本高昂(高功率激光器價格昂貴)。
切割速度遠低于切割同等厚度鋼材。
切割質量(特別是斷面垂直度、粗糙度)通常不如切割鋼材或采用其他方法切割銅。
2.使用綠光或紫外激光器:
原理:更短波長(如綠光532nm、紫外355nm)的激光被銅的吸收率顯著提高(可超過50%)。
局限:
設備成本極其昂貴。
功率水平通常較低(遠低于光纖/紅外激光)。
主要用于精密微加工(鉆孔、劃線、雕刻薄箔),幾乎無法用于工業級厚度的切割。
加工速度慢。
3.特殊工藝與輔助手段:
表面處理:在銅表面涂層(如黑漆、專用吸光材料)或做氧化處理(發黑),暫時提高其對激光的吸收率。
局限:增加工序和成本;涂層可能污染材料或需要后續清理;效果不穩定;不適用于大批量或高精度要求。
改變輔助氣體:嘗試使用氧氣等活性氣體,利用氧化反應放熱來輔助切割。
局限:效果有限,對高反射高導熱問題改善不大,且會在切割面形成較厚的氧化層,通常不適用于需要潔凈切割面的場合。
四、更優選擇:替代加工技術
鑒于激光切割銅的重重困難與風險,其他加工方法通常是更可靠、更經濟、更安全的選擇:
1.等離子切割:
利用高溫高速等離子弧熔化金屬,并用高速氣流吹走熔融物。
優點:切割銅(尤其是中厚板)速度較快,成本相對較低,設備普及度高,不受材料反射率影響。
缺點:切割精度和切口質量通常不如激光切割鋼材(切縫較寬,斜角較大,熱影響區大),毛刺較多,噪音大,煙塵多。
2.水刀切割:
利用超高壓水射流(或混合磨料)進行切割。
優點:冷切割,無熱影響區、無變形、無材料性質改變;可切割任意厚度的銅;無反射風險;切割精度高。
缺點:切割速度相對較慢;設備投資和運行成本(能耗、磨料)較高;切割厚硬材料時可能產生輕微錐度。
3.沖壓/剪切:
適用于大批量、形狀相對簡單的薄銅板零件。
優點:效率極高,成本低。
缺點:模具成本高,柔性差,不適合復雜輪廓或小批量。
4.線切割:
利用電火花腐蝕原理進行切割。
優點:可切割高硬度導電材料,精度極高,表面質量好。
缺點:切割速度很慢,主要用于精密模具加工,不適合大批量生產。
結論:理解限制,明智選擇
激光切割機難以切割銅的核心癥結在于銅的超高反射率、卓越導熱性以及由此引發的加工效能低下和嚴重安全風險。雖然超高功率光纖激光器提供了一種有限的解決方案(主要用于薄銅板),但其成本高昂、反射風險仍需嚴防、切割質量和厚度能力受限。安全因素(反射激光的破壞性)始終是激光切割銅的首要制約。
因此,在需要加工銅材時,務必優先考慮等離子切割、水刀切割、沖壓或線切割等替代工藝。這些技術在效率、成本、安全性或加工能力方面,往往比強行使用激光切割更具綜合優勢。理解材料特性與加工技術的匹配關系,是做出最優決策、保障安全和效率的關鍵。銅的“高反”特性,讓它成為了激光切割王國中一塊名副其實的“硬骨頭”,也促使制造者不斷探索更適配的加工之道——這既是挑戰,也是驅動技術革新的動力。
點擊右側按鈕,了解更多激光打標機報價方案。
免責聲明
本文內容通過AI工具智能整合而成,僅供參考,博特激光不對內容的真實、準確或完整作任何形式的承諾。如有任何問題或意見,您可以通過聯系[email protected]進行反饋,博特激光科技收到您的反饋后將及時答復和處理。